3D laser cutting
- Cesar Zarate
- 18 nov 2015
- 2 Min. de lectura
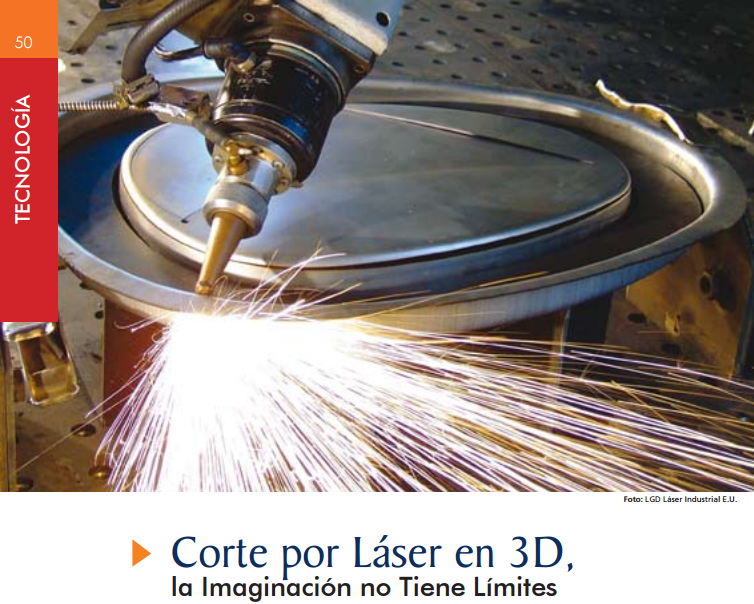
Operation Laser Technology
The laser effect is generated by exciting the molecules of the substance "active laser", ie, those that emit laser radiation as CO2, crystal ruby crystal mixtures of neodymium, aluminum oxide, yttrium garnet-NdYag-Laser, such excitation can be done by high frequency (HF) electric shock (DC) or pulsed light. The substance is subjected to excitation in a physical environment called resonator. Initially, the laser beam is conveyed from the resonator to the cutting head by special lenses and focused on an area covering between 0.1 to 0.3 mm diameter, which is located on the material surface to a few tenths of a millimeter East. Laser cutting can be 100 percent energy: in this case the intense heat of the concentrated laser beam melts the material to work (typically stainless steel or aluminum) in a very narrow area-usually between 0.2 mm or less. Next, a flow of gas (air or nitrogen) which acts together with the laser beam, the molten ejected from the bottom of the sheet material, and finally the cutting area must move in the sheet working to produce the profile cutting required. Likewise, the cutting can include an oxidation process (in the case of carbon steels) in which oxygen is the gas cutting. The cutting head, the sheet to be processed, or both can be moved depending on the design of the machine. The infrared light generated by CO2 laser-light that is invisible to the human eye behaves like a beam of light "normal" that may be reflected by mirrors and focused by lenses made of special materials, is thus achieved as cut laser material. (See Table: Generation Laser Beam).
Cutting process
After defining the geometry of the cuts and the process by programming software, this information is passed to control through CNC machine system, which automatically performs all the operations required in the sequence are scheduled. Subsequently, the workpiece and the support should be placed on the bed cutting and specify the program reference point where it is located and already taking the path and the generated code, the machine is ordered to start the cutting process specified on the screen. The program provides the facility that is listed after the figure, the file can be saved and at the time required, can be reused, which relaxes the system it is not necessary to manufacture large quantities of parts but only necessary.
Auto
Current metal
Font
Luís Gabriel Díaz. Ingeniero electromecánico. Propietario LGD Láser Industrial E.U. ldiaz@laser3lc.com
Jaime Guerrero. Ingeniero. Consultor Técnico. Makser Ltda. j.guerrero@ makserweb.com
Comments